El punzonado en punzonadoras de CNC es una operación mecánica automatizada con la cual mediante herramientas especiales (punzones) aptas para el corte se consigue realizar agujeros en chapas (separar una parte metálica de otra obteniéndose una figura determinada).
Contáctenos:
Contáctenos y con gusto le ayudaremos a resolver cualquier requerimiento de metalmecánica.
Tenemos un equipo de diseño y técnico altamente capacitado, así como maquinaria y planta industrial de alta capacidad.
Dirección: Felipe Landaverde 100, San Juan, Iztapalapa, 09830 Iztapalapa, CDMX.
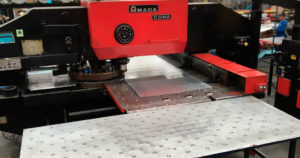
Los elementos básicos (juego) para realizar un agujero en una chapa son
- Punzón
- Pisador (o separador)
- Matriz
Para poder realizar el agujero de una forma y unas dimensiones determinadas estos elementos debe tener la misma forma.
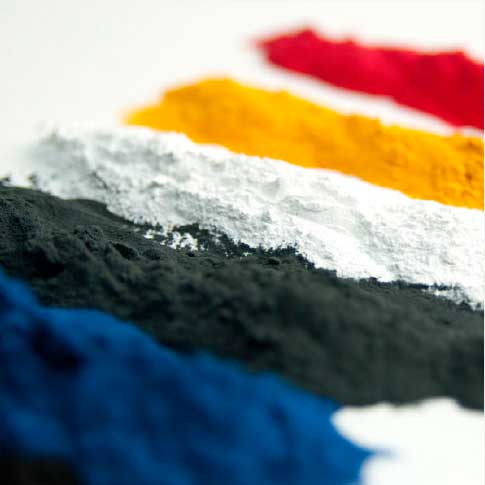
¿Cómo funcionan las punzonadoras CNC?
Hoy en día, podemos segmentar las punzonadoras CNC en dos bloques. Estos dos bloques se caracterizan por las funciones de cada uno.
Por un lado tenemos las punzonadoras de torreta. Éstas tienen un doble tambor donde se alojan los utillajes de punzonado.
Ese utillaje está formado por un porta punzón, es decir, un contenedor. Éste está montado en la torreta superior, que contiene una guía, el muelle, un pisador y, evidentemente, el punzón.
En la torreta de debajo se monta la matriz y gira en función del programa que seleccionemos. De esta forma se eligen los utillajes que se necesitan para realizar la pieza.
Por otra parte, nos encontramos con las punzonadoras de monopunzón. Éstas contienen un almacén de utillaje. La propia punzonadora irá tomando y dejando los utillajes del almacén.
Tienen un casete en cada una de las posiciones del almacén donde se alojan el punzón, la matriz, el punzón y un anillo de orientación.
Aquí un ejemplo de cómo se fabrican multitud de piezas con la máquina punzonadora hidráulica. VIDEO cortesía de nuestros amigos de Nargesa:
Qué elementos son necesarios para realizar un agujero con una punzonadora
Para que podamos realizar un agujero en la chapa con nuestra punzadora necesitamos una serie de elementos básicos. Éstos son el pisador o separador, la matriz y, evidentemente, el punzón. A este trío se le llama “juego”.
Cómo es el ciclo de punzonado
Para punzonar de forma correcta y realizar el agujero tal y como queremos, en forma y tamaño, el juego (ese trío de punzón, pisador y matriz) tiene que tener la misma forma.
En ambos bloques antes mencionados, el ciclo de punzonado es similar y la chapa siempre debe ir entre la matriz y el punzón.
En una punzonadora de torreta, la propia torreta girará dejando el utillaje a la altura del martillo, que descenderá empujando al portapunzón.
- El pisador tomará contacto con la chapa presionándola e inmovilizándola, para poder realizar el agujero con precisión.
- El punzón irá descendiendo cuando el martillo comprima los muelles del portapunzón. En ese momento, comenzará a tomar contacto con la chapa.
- Tras ello, el punzón comenzará a agujerear la chapa tanto en la parte inferior como en la superior. Cuando coincidan, el retal correspondiente a la incisión quedará suelto.
- Por último, el martillo ascenderá otra vez retirando el punzón de la chapa , mientras el pisador sigue manteniéndola plana.
Por contra, nos encontramos con el otro tipo de punzonadora, que funciona de forma más simple. Las dos principales diferencias entre ambas son:
- El separador esta vez no presiona la chapa mientras se realiza la punción, pero se mantiene a muy poca distancia de la superficie superior de la misma.
- Por otro lado, en este caso es el propio martillo el que estira el punzón para sacarlo de la chapa. Al estar tan cerca, el separador mantiene la chapa quieta.
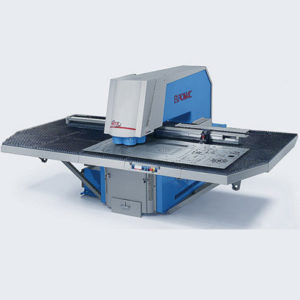
Punzonado con punzonadoras CNC
Actualmente en el mercado podríamos clasificar las punzonadoras CNC en dos tipos en función del tipo utillaje que utilicen: las punzonadoras de torreta y las monopunzón.
Las primeras tienen un doble tambor (torreta superior e inferior) donde van alojados los utillajes de punzonado. El utillaje se compone de un contenedor (porta-punzón) que va montado en la torreta superior y que consta de una guía, un muelle, el punzón y el pisador.
En la torreta inferior se montará la matriz. Esta torreta girará en función del programa para ir seleccionando los utillajes necesarios para realizar la pieza.
El segundo tipo de punzonadora tienen un almacén de utillaje. La punzonadora ira cogiendo y dejando los utillajes de ese almacén. Cada una de las posiciones del almacén dispone de un cassette donde están montados el punzón, el separador, la matriz y un anillo de orientación.
Los elementos básicos para realizar un agujero en una chapa son el punzón, el pisador o separador y la matriz. A estos tres elementos se les denomina juego.
Antes de entrar a valoras los diferentes aspectos que influyen en estos elementos analizaremos la geometría de un agujero realizado en la chapa por estos elementos.
Ciclo de punzonado
Para poder realizar el agujero de una forma y unas dimensiones determinadas el juego (punzón, matriz y pisador) debe tener la misma forma. El ciclo de punzonado en ambos tipos de punzonadora es muy similar y la chapa debe estar siempre entre el punzón y la matriz.
En una punzonadora de torreta la punzonadora hará girar la torreta y situará el utillaje justo debajo del martillo de la máquina.
A partir de ese momento el martillo descenderá empujando al porta-punzón. El pisador contactará con la chapa presionando y sujetando la chapa manteniéndola plana contra la matriz.
El martillo seguirá bajando, comprimiendo los muelles del porta-punzón y haciendo descender al punzón. El punzón iniciará la penetración en la chapa produciendo una pequeña curvatura en la chapa alrededor del filo cortante del punzón y de la matriz.
Seguidamente se iniciará una fase de corte que posteriormente se convertirá en unas fracturas en la chapa tanto en la parte superior como inferior debido al arranque del material. Cuando coincidan las fracturas anteriores el retal correspondiente al agujero quedará suelto de la chapa.
El martillo seguirá bajando hasta su limite inferior para facilitar la caída del retal. A continuación el martillo subirá y los muelles del contenedor extraerán el punzón de la chapa mientras el pisador mantiene la chapa completamente plana.
En el otro tipo, la punzonadora deberá dejar el punzón situado debajo del martillo en su lugar del almacén e ir a buscar el utillaje deseado.
La diferencia principal en el ciclo de punzonado es que el separador no presiona la chapa mientras el punzón está agujereando la chapa pero se mantiene a muy poca distancia de la superficie superior de la chapa. Otra diferencia es que es el propio martillo el que estira el punzón para sacarlo de la chapa.
El separador actúa reteniendo la chapa cuando esta tiende a subir junto con el punzón.
Estas 4 zonas son las que determinarán la calidad de un agujero punzonado. La calidad del agujero vendrá condicionada por las características y condiciones del punzón, de la matriz y del pisador.
Tolerancia de corte de la matriz
Para realizar un agujero de una dimensión concreta en una chapa de un espesor determinado el punzón debe tener la misma dimensión que el agujero deseado y la matriz deberá tener una dimensión un poco mayor. Esa diferencia de dimensiones es conocida como tolerancia de corte de la matriz.
Es muy importante que la tolerancia de corte de la matriz este uniformemente repartida alrededor de la medida del punzón incluso en las esquinas.
Por ejemplo, si un punzón es de diámetro 10 mm y la matriz es de 10,2 mm la tolerancia total de 0,2 mm a de quedar uniformemente repartida de forma que entre pared de punzón y pared de matriz se mantenga una tolerancia de 0,1 mm. en todo el perímetro.
La tolerancia de corte adecuada (figura 3) es aquella que hace coincidir las fracturas de corte generadas por el punzón y por la matriz. Esto ocurrirá cuando las fracturas se encuentren a 1/3 o 1/2 del espesor de la chapa.
Si utilizamos una matriz con tolerancia demasiado ajustada se crearán dos fracturas que no se encontrarán. Esto es fácilmente apreciable ya que la zona brillante del agujero y del retal es mayor.
Por otro lado al ser la tolerancia menor implicará que sea necesario mayor fuerza para cortar por lo que el utillaje puede sufrir un mayor desgaste. Una tolerancia demasiado pequeña podría llegar a crear más rebabas por laminación. Otro inconveniente es que a menor tolerancia es necesario mayor fuerza de extracción.
Si utilizamos una tolerancia demasiado grande (Figura 4) se generará una curvatura mayor alrededor del agujero y las rebabas serán mayores.
En el agujero y en el retal se observará que la zona de corte (zona brillante) es más pequeña mientras que la zona de arranque de material es mayor. La tolerancia de corte adecuada de una matriz varía con el espesor y con el tipo de material de la chapa. Normalmente se obtiene de un porcentaje con relación al espesor de la chapa.
Como regla general se puede establecer que a mayor esfuerzo de corte del material y mayor espesor de chapa la tolerancia de corte debe ser mayor.
Por ejemplo, para chapas de un mismo espesor se necesitará una tolerancia de corte mayor para el inoxidable que para una de acero o de aluminio. Por otro lado una chapa de 6 mm. de espesor necesitará más tolerancia que una chapa de 1 mm.
Los valores de la tolerancia pueden variar desde un 15% a un 25% del espesor de material en función del espesor y tipo de material. Como regla general se podría aplicar como tolerancia de corte un 15% para el aluminio, un 20% para el acero y un 20-25% para el inoxidable.
A continuación mostramos una tabla en la cual se sugieren unas tolerancias de corte orientativas para el punzonado de diferentes materiales.
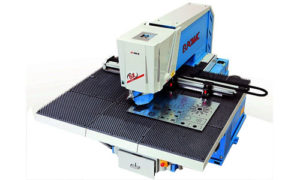
Queda claro que utilizar una tolerancia de corte adecuada es muy importante. Resumiendo, podríamos concluir citando los beneficios de utilizar una tolerancia de corte adecuada:
- Menor rebaba y curvatura en los agujeros
- Agujeros más uniformes y cortes más limpios
- Piezas punzonadas más planas, con menos deformaciones
- Mayor precisión entre agujeros
- Mayor vida del utillaje (punzón y matriz)
- Mejor extracción del punzón
- Menor adhesión del material punzonado en las paredes del punzón
Contáctenos:
Contáctenos y con gusto le ayudaremos a resolver cualquier requerimiento de metalmecánica.
Tenemos un equipo de diseño y técnico altamente capacitado, así como maquinaria y planta industrial de alta capacidad.
Dirección: Felipe Landaverde 100, San Juan, Iztapalapa, 09830 Iztapalapa, CDMX.
Problema de subida de retales
La tecnología de las nuevas punzonadoras permite que estas puedan dar muchos golpes por minuto. Estas altas velocidades de punzonado pueden provocar que el retal del agujero punzonado tienda a subir hacia arriba.
Esto puede provocar varios problemas en una punzonadora CNC. Dependiendo de la posición del retal puede ocasionar que la chapa al desplazarse se trabe con el propio retal moviéndose o saliéndose de las mordazas que la sujetan.
Esto puede ocasionar desde un mal posicionamiento de los agujeros posteriores a que la chapa colisione con algún elemento de la máquina ocasionando daños. También se dan situaciones en los que el retal sale completamente de la matriz.
En este caso el riesgo es que el retal quede situado en la arista de corte de la matriz ocasionando daños en el utillaje durante el siguiente punzonado ya que en una zona de corte tendríamos el doble del espesor de chapa. Esto ocasionará daños al utillaje teniendo, en el mejor de los casos, que rectificar punzón y matriz.
En el mercado existen matrices con un mecanizado especial en su interior para evitar que los retales puedan subir, son las matrices Slug Free. Estas matrices (ver figura 2) están mecanizadas interiormente con una doble conicidad. Cuando el retal es separado de la chapa el punzón sigue bajando.
Como el mecanizado interior de la matriz se va reduciendo (centésimas) obliga al retal a comprimirse. Una vez que el retal pasa el punto de máxima compresión la conicidad de la matriz cambia y el retal, por elasticidad, tiende a recuperar su dimensión original.
En ese momento será muy difícil que el retal pueda subir hacia arriba y facilitando la caída libre del retal. Existen también otros motivos que pueden provocar la subida de retales punzonados. Para evitar estos problemas citamos algunas medidas preventivas:
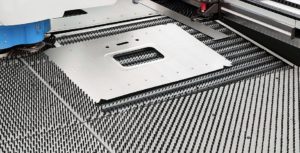
- Utilizar matrices Slug Free para facilitar la caida del retal
- Desmagnetizar los utillajes después de rectificarlos. Cuando se rectifican utillaje a veces se suele utilizar platos magnéticos para fijarlo. Esto puede provocar que se magnetice el utillaje. Cuando se punzonan materiales férricos el utillaje puede actuar como un imán atrayendo los retales
- Disminuir la tolerancia de la matriz. De esta forma se reduce la apertura por donde salen los retales, reduciendo la probabilidad de que estos puedan subir fácilmente.
- Aumentar la penetración del punzón en la matriz llevando el retal lo más abajo posible. Esto es importante junto con el punto anterior cuando se punzona material protegido con plástico. De esta forma aseguraremos que el plástico se pueda romper en todo el perímetro del agujero.
- Utilizar rectificados especiales en el punzón. De esta forma el retal no quedará plano y se pueden evitar el efecto ventosa y por otro lado obligará a aumentar la penetración del punzón
- Utilizar eyectores de uretano en el punzón. Los eyectores están situados en la superficie de corte de los punzones. Actúan como expulsores ya que estos se comprimen al inicio del ciclo de punzonado y cuando el retal ya está suelto de la chapa lo impulsan hacia abajo
- Utilizar la lubrificación automática de utillaje (ABS). El sistema ABS de algunas máquinas, basado en inyectar aceite pulverizado, ayuda a evitar que el retal pueda subir debido a la propia presión de aire.
Problemas de afilado y vida del utillaje
¿Cuántos golpes puedo dar antes de rectificar un punzón o matriz? Esta es la típica respuesta cuya respuesta es muy difícil de dar. El motivo es que existen muchas variables para poder dar una respuesta concreta.Uno de esos factores es el espesor y el tipo de chapa que se esté punzonando. Esta claro que la fuerza necesaria para punzonar aluminio de 1 mm no es la misma que para punzonar 4 mm de inoxidable. Cuanta más fuerza sea necesaria más se desgastará el utillaje.
Otro factor es el uso correcto de las tolerancias del cual ya hemos hablado anteriormente. Si las tolerancias no son correctas y las fracturas no se encuentran el utillaje deberá realizar más esfuerzos para realizar un agujero.
Se comento también que la tolerancia debe estar uniformemente repartida y partiendo de que el utillaje está bien mecanizado (centrado y orientado) el problema puede ser de la máquina. Puede existir un problema de alineación entre punzón y matriz achacable a la punzonadora.
Como problemas de alineación se puede dar el caso de que los centros del punzón y de la matriz no coincidan y/o que la posición angular de estos no sea correcta.
Se podría dar el caso que el problema sea de las chavetas/chaveteros de la máquina, porta-punzones o cassettes un mal montaje por parte del operario o que el mecanismo del index, que permite girar los utillajes este desfasado entre punzón y matriz.
También es importante para la vida del utillaje lubrificar los punzones, las guías y la chapa. Esta demostrado, y de hecho en algunas punzonadoras es standard y en otras opcional, que la lubrificación del utillaje (ABS) aumenta la vida del utillaje. También en muchas punzonadoras se puede instalar un sistema de lubrificación de la chapa.
Mecanizar radios de construcción en las esquinas de los utillajes puede aumentar la vida de los utillajes. Por ejemplo en ciertas esquinas de algunos triángulos o en esquinas de cuadrados o rectangulares cuando se está punzonando chapa de cierto grosor.
Para ciertas aplicaciones es posible aumentar la vida del utillaje aplicando afilados especiales a los punzones. También se les pueda nitrurar o aplicarle un recubrimiento que aumente su dureza y reduzca el coeficiente de fricción.
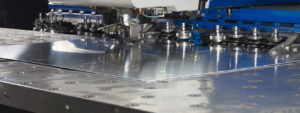
Pero lo más importante de todo en condiciones de funcionamiento adecuadas de máquina para mejorara la vida de los utillajes es mantenerlos en las mejores condiciones de corte posibles.
Para ello es necesario rectificarlos frecuente y adecuadamente. La recomendación habitual a la hora de rectificar un utillaje es tener que rectificar unos 0,25 mm. Esto quiere decir que tanto en el punzón como en la matriz el filo de corte se ha convertido en un radio de 0,25 mm.
Hay que tener en cuenta que cada vez que se da un punzonado se crea un microradio debido al desgaste.
Esta claro que al realizar el siguiente punzonado las condiciones de corte son un poquito peores que en el punzonado anterior. Esto obligará a ejercer un poquito más de fuerza para poder realizar el agujero, por lo tanto, el punzón se desgastará un poquito más que en el punzonado anterior.
Quede claro que este desgaste entre un punzonado y el siguiente es inapreciable pero a fuerza de ir acumulando punzonados el desgaste va creciendo rápidamente.
Cuando se crea un radio de 0,25 mm en el filo de corte hemos realizado 100.000 golpes. Si rectificamos 0,25 mm estaremos en condiciones óptimas de punzonado y podremos dar 100.000 golpes más. Siguiendo este procedimiento cuando hayamos rectificado hasta 1 mm habremos dado 400.000 golpes.
Supongamos que después de que el filo de corte del punzón se haya redondeado a un radio de 0,25 mm no afilamos el utillaje.
Al no estar en las mejores condiciones de corte el utillaje cuando tuviese que rectificarse 0,5 mm (0,25 más que antes) dará 50.000 golpes. Si seguimos este procedimiento el numero de golpes correspondiente para cada afilado de 0,25 mm más será menor. En total, cuando tuviésemos que rectificar un total de 1 mm habremos dado 185.000 golpes.
Observamos que depende del procedimiento de rectificado que sigamos podemos dar el doble de golpes. En resumen, un buen mantenimiento del utillaje puede alargar mucho la vida de los utillajes y que es el mejor remedio para alargar la vida del utillaje.
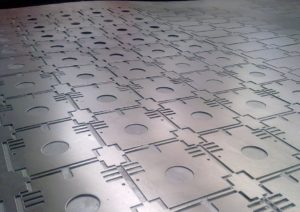
¿Qué es una punzonadora CNC y cuáles son sus características?
Las punzonadoras de CNC son máquinas automatizadas con la cual mediante herramientas especiales se logra conseguir cortes y realizar agujeros en chapas obteniendo una figura determinada.
La fabricación de estas estructuras metálicas son hechas por expertos en la materia, así como los más variados diseños de perforación requeridos por los clientes, por más complicada figura que esta sea, ellos logran realizar figuras perfectas con la rotación de unos 360° del punzón y los rápidos cambios de la herramienta.
¿Cómo funciona la punzonadora CNC?
Según su función se dividen en dos tipos, las punzonadoras de torreta y las monopunzón. La punzonadora de torreta tiene un doble tambor (torreta superior e inferior) donde van alojados los utillajes de punzonado.
El utillaje se compone de un contenedor que va en la torreta superior y que consta de una guía, un muelle, el punzón y el pisador. La torreta inferior se montara en la matriz, y girara en función del programa para ir seleccionando los utillajes necesarios para realizar la figura.
La punzonadora monopunzón, tiene un almacén de utillaje que irá cogiendo y dejando los utillajes en ese almacén. Cada una de las posiciones del almacén dispone de un cassette donde están montados el punzón, el separador, la matriz y un anillo de orientación.
Los elementos básicos para realizar un agujero en una chapa son el punzón, el pisador o separador y la matriz.
Características
- La punzonadora CNC se utiliza para procesar y punzonar placas con una alta precisión y eficiencia.
- Incorpora un sistema internacional de control numérico de alto rango, garantizando un acabo de calidad.
- Permite una detección, protección y autodiagnóstico automático.
- Tiene alta flexibilidad, tiempo corto de la depuración de la matriz, alta automaticidad y capacidad de procesar placas de gran tamaño.
- También cuenta con una fijación flotante y una plataforma operativa con bolas de acero y cepillos.
- Se caracteriza por un posicionamiento lateral preciso y una guía excelente, es amplia y muy estable en tipo cerrado.
Ventajas
- Ahorro de mano de obra, procesa una placa entera y alimenta automáticamente los materiales.
- Ahorro del tiempo de computarización, realiza una transferencia y procesamiento automático del diagrama CAD.
- Ahorro de tiempo en el cambio de matriz, incorpora un mecanismo de cambio de matriz a alta velocidad.
- Mejora la producción, con una eficiencia de producción de 6 o 7 veces.
- Coeficiente de alta seguridad, la realización de un proceso desatendido puede evitar al máximo peligros potenciales.
El servicio de punzonado CNC es muy utilizado en las empresas metalúrgicas, ya que desempeña un papel muy destacado en la industria de placas de metal.
Su alta automaticidad, alta precisión y eficiencia, rendimiento estable, seguridad y fiabilidad hacen que el producto sea 100% de calidad brindando magníficos resultados.
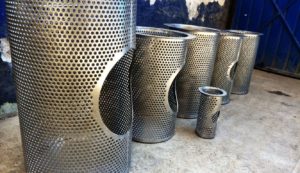
Servicio de Punzonado CNC
Con la rotación de 360° del punzón y los rápidos cambios de herramienta, se pueden realizar prácticamente cualquier tipo de láminas perforadas especiales o cualquier figura por complicada que esta sea, así como los más variados diseños y acomodos de perforación requeridos por nuestros clientes.
Contáctenos:
Contáctenos y con gusto le ayudaremos a resolver cualquier requerimiento de metalmecánica.
Tenemos un equipo de diseño y técnico altamente capacitado, así como maquinaria y planta industrial de alta capacidad.
Dirección: Felipe Landaverde 100, San Juan, Iztapalapa, 09830 Iztapalapa, CDMX.
Contenido: